Cold chain packaging is an essential process that involves the transportation and storage of temperature-sensitive products such as pharmaceuticals, biologics, and food products, among others. The cold chain packaging process is crucial because it ensures that the products are kept at the required temperature range throughout the supply chain, from manufacturing to distribution, to the end consumer. However, the process is not without its challenges, and companies must implement best practices to ensure the products are protected from temperature excursions, which can lead to product spoilage, reduced efficacy, and patient harm.
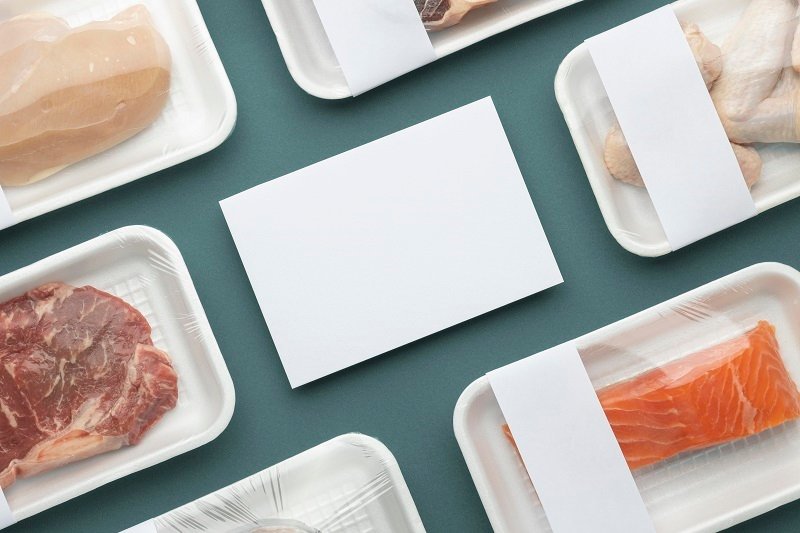
In This Article, We Will Discuss The Challenges Faced In Cold Chain Packaging And The Best Practices That Companies Can Adopt To Overcome Them.
Challenges In Cold Chain Packaging:
Temperature Excursions:
Temperature excursions occur when the temperature of a product deviates from the recommended temperature range. This can occur during transportation or storage due to various reasons such as mechanical failures, power outages, and incorrect handling. Temperature excursions can cause product spoilage, reduced efficacy, and in severe cases, patient harm.
Packaging Design:
Cold chain packaging is designed to maintain the required temperature range for the product during transportation and storage. However, designing the right packaging can be a challenge as it must consider various factors such as the product’s sensitivity to temperature, the duration of transportation, and the shipping conditions.
Monitoring and Control:
Monitoring and controlling the temperature of products during transportation and storage is critical to ensuring product efficacy and patient safety. However, monitoring the temperature of products can be a challenge, especially when products are transported across different regions, where temperature variations are prevalent.
Compliance:
Compliance with regulatory requirements is a significant challenge in cold chain packaging. Companies must ensure that their cold chain packaging processes comply with regulations such as the Good Distribution Practices (GDP) and the International Air Transport Association (IATA) regulations.
Insufficient Infrastructure:
In some regions, especially in developing countries, there may be an insufficient infrastructure for cold chain packaging. This can include a lack of refrigerated trucks, cold storage facilities, and reliable power supply, among other things. In such cases, companies may need to invest in infrastructure or develop alternative cold chain packaging solutions to ensure the safe transportation and storage of their products.
High Costs:
Cold chain packaging can be expensive due to the specialized packaging, monitoring systems, and transportation infrastructure required. This can be a significant challenge for small and medium-sized enterprises, as the high costs may be prohibitive for them. Companies may need to explore cost-effective solutions while still maintaining the required temperature range for their products.
Supply Chain Complexity:
The cold chain packaging process is part of a broader supply chain that can be complex, especially when products are transported across different regions and countries. This complexity can make it difficult to maintain the required temperature range for products and monitor their temperature effectively. Companies may need to work with their logistics partners to develop effective supply chain solutions that ensure product safety and efficacy.
Seasonal Temperature Variations:
Temperature variations can be more extreme during certain seasons, such as summer and winter, which can be a challenge for cold chain packaging. For example, in summer, the temperature inside a truck can rise quickly, making it difficult to maintain the required temperature range for products. Companies may need to take additional precautions during such seasons, such as using more effective insulation, increasing the frequency of temperature monitoring, and adjusting the transportation routes and schedules.
Best Practices In Cold Chain Packaging:
Develop a Comprehensive Cold Chain Packaging Plan:
Developing a comprehensive cold chain packaging plan is critical to ensuring that products are protected from temperature excursions. The plan should include details such as the temperature range for the product, packaging design, monitoring and control procedures, and contingency plans for temperature excursions.
Use Qualified Packaging:
Qualified packaging is packaging that has been tested and validated to maintain the required temperature range for a product during transportation and storage. Companies should use qualified packaging that is suitable for the product’s sensitivity to temperature and the duration of transportation.
Implement Monitoring and Control Procedures:
Monitoring and controlling the temperature of products during transportation and storage is critical to ensuring product efficacy and patient safety. Companies should implement monitoring and control procedures such as using temperature data loggers and real-time monitoring systems.
Train Personnel:
Training personnel on the cold chain packaging process is critical to ensuring compliance with regulatory requirements and the proper handling of products. Companies should provide training to personnel involved in the cold chain packaging process, including drivers, warehouse staff, and quality control personnel.
Develop Contingency Plans:
Developing contingency plans for temperature excursions is critical to ensuring that products are protected in the event of an excursion. Contingency plans should include procedures for identifying temperature excursions, taking corrective action, and ensuring that affected products are not distributed to customers.
Ensure Compliance with Regulatory Requirements:
Compliance with regulatory requirements such as the Good Distribution Practices (GDP) and the International Air Transport Association (IATA) regulations is critical to ensuring product safety and efficacy. Companies should ensure that their cold chain packaging processes comply with regulatory requirements and that personnel are trained on compliance.
Proper Handling:
Proper handling of cold chain products is critical to maintaining their efficacy. Companies should provide training to personnel on proper handling and storage procedures, including how to handle products, monitor temperature, and maintain the cold chain. This can help ensure that products are not exposed to temperature excursions and maintain their efficacy throughout the supply chain.
Quality Control:
Quality control is an essential aspect of cold chain packaging. Companies should establish quality control procedures that cover all aspects of the cold chain, from packaging design to transportation and storage. This can include regular inspections, testing, and audits of the cold chain process to identify and mitigate potential risks to product quality and safety.
Data Management:
Effective data management is critical for monitoring the cold chain and identifying potential issues that could affect product safety and efficacy. Companies should implement data management systems that capture and analyze temperature data, allowing them to identify temperature excursions and take corrective action quickly. This can help ensure that products remain within the required temperature range throughout the supply chain.
Risk Management:
Risk management is essential for mitigating potential risks to product quality and safety. Companies should conduct risk assessments to identify potential risks in the cold chain process, including packaging design, transportation, and storage. They should then develop risk management plans that outline how to mitigate and manage these risks effectively.
Collaboration:
Collaboration is critical for ensuring the safe and efficient transportation and storage of temperature-sensitive products. Companies should work closely with their logistics partners to develop effective cold chain solutions that meet the specific needs of their products. This can include collaborating on packaging design, transportation routes and schedules, and temperature monitoring and control procedures.
Industries That Commonly Use Cold Chain Packaging:
Pharmaceutical and Biotech:
Vaccines, medications, and biological products are examples of products that require cold chain packaging to maintain their efficacy.
Frozen Food:
It is also an industry that heavily relies on cold chain packaging. Frozen food products such as frozen vegetables, fruits, meat, seafood, and bakery products must be stored and transported at very low temperatures to prevent spoilage and maintain quality.
Chemical and Life Science:
Chemicals and laboratory specimens are examples of products that require cold chain packaging to maintain their stability and effectiveness.
Cosmetics and Personal Care:
Products such as skincare, haircare, and fragrances require cold chain packaging to maintain their quality and efficacy.
Agriculture:
Fresh fruits and vegetables, flowers, and live plants require cold chain packaging to maintain their freshness and shelf life.
Conclusion:
Cold chain packaging is a critical process that ensures temperature-sensitive products such as pharmaceuticals, biologics, and food products, among others, are protected from temperature excursions during transportation and storage. To overcome these challenges, companies must adopt best practices, including developing a comprehensive cold chain packaging plan, using qualified packaging, implementing monitoring and control procedures, training personnel, developing contingency plans, and ensuring compliance with regulatory requirements. By partnering with experienced designers of cold chain packaging solutions, companies can overcome the challenges of cold chain packaging and ensure that their products remain safe and effective throughout the supply chain.